Wedge Wire Water Intake Design Considerations
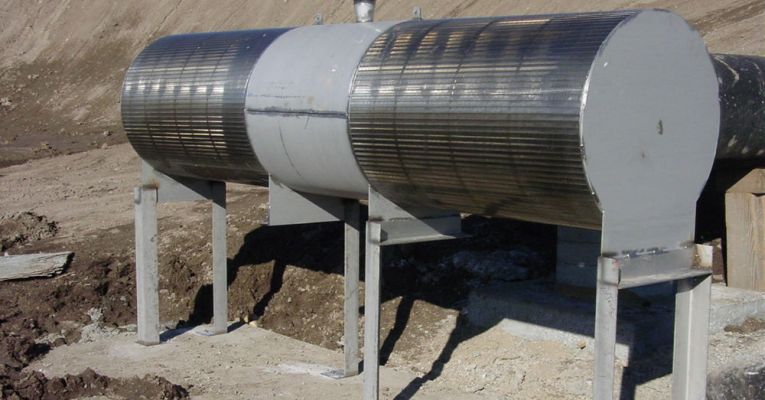
When designing an intake system, the water intake screen is a critical element to a well-designed system. The entire water intake system is dependent on the functionality of the water intake screen in order to work correctly. If the screen is designed properly, it leads to an efficient system that will reduce maintenance costs over the system’s lifespan. However, cost savings isn’t the only consideration to a good design.
Key qualities of a properly designed water intake system:
• Meets the requirements of the operating environment
• Provides operational efficiency
• Minimizes head loss in the intake system
• Meets EPA 316(b) requirements
• Protects aquatic life
In order to design a water intake screen that effectively meets all these capabilities, there are fundamental design recommendations to consider. With Hendrick Screen’s 40-plus years of experience manufacturing water intake screens, we’d like to share what we learned about successful designs.
Early Involvement of the Screen Manufacturer
Working with the screen manufacturer early in the design phase will prevent issues that can develop later. Tapping into the experience of the screen manufacturer will assure that you choose the correct intake design, size it and locate it correctly, and identify any special requirements that need to be built into the screen. In addition, the manufacturer can provide preliminary budgets so that the project costs are planned correctly. Reviewing these design requirements with the screen manufacturer early can eliminate expensive and extreme rework due to installing an improper design.
Understand the Types of Intakes
There are several different types of intake screens on the market. Knowing the types of screens and their benefits can help you design the most efficient system. The three most common are:
- Drum Screen: Drum screens are used in quiet waters where the water current passing the screen is minimal. This would include lakes and reservoirs where water conditions are stable and have a low velocity water flow. Drum screens are also ideal for tight spacing conditions. The screens can be mounted vertically or horizontally to prevent debris from collecting on the screened surface. The drum screen is also the most economical form of intakes.
- T-intake Screen: The most common installation is for a T-intake screen. They are often designed for cooling plants, pulp and paper mills, and other industrial facilities that require the intake of large amounts of water from lakes, rivers or oceans. T-intakes are designed to withstand multiple water conditions including the harshest environments. Screen manufacturers offer flexibility in the design of the T-intake to accommodate special conditions where the unit will be installed. For example, the intake screen can be designed with a conical end to deflect debris that flows toward it (also see Early Involvement of the Screen Manufacturer).
- Half-Barrel Screen: The half-barrel screen is designed for shallow water conditions, it provides the same screen flow characteristics as a larger T-intake screen. However, its half-size allows it to be placed on the bottom of streams and rivers where a T-intake wouldn’t work.
Water Depth
The depth of the water at the desired location for the intake’s installation is one of the many factors considered when properly sizing an intake screen. A T-intake or drum screen requires 2-times the diameter of the minimum water depth. A half-barrel only requires a submergence level of six inches. The maximum submergence level needs to be accounted for in the design of the intake to accommodate the water pressure at the installation site. Finally, if there are inconsistent water depths at the intake’s location, multi-level intakes are an option to allow flexibility.
Material Type
There are four basic water conditions that can determine the material for an intake screen.
- Freshwater with no biofouling issues: 304 Stainless Steel provides the most economical material in freshwater conditions.
- Brackish water: 316 Stainless Steel is recommended to increase corrosion resistance.
- Freshwater with biofouling concerns: 90/10 Copper Nickel offers excellent anti-biofouling properties (e.g., Zebra or Quagga Mussels) in freshwater.
- Saltwater: 70/30 Copper Nickel is not only corrosion resistant in saltwater, but it also prevents biofouling.
Capacity
When a manufacturer prepares to design a water intake screen, they should ask you three very important questions that will contribute to the success of the system:
How much intake capacity is currently required? – This is the minimum capacity that needs to be designed to meet the current water demands.
Does redundancy need to be included in the design? – Redundancy is needed to meet the water demands with an allowed percentage of blinding between airburst cleaning cycles.
Are there future plans for expansion that will require additional capacity? – If increased water demands are going to be required, this can be considered for the current design so that the intake screen can handle the additional capacity when needed.
Understanding and following these helpful guidelines will provide a good starting point to develop an efficient water intake screen. Early communications with the intake screen manufacturer will help you tap into their expertise to develop a screen that will provide operational reliability under all conditions for years to come.