False Bottom Screens For Brewing And Distilling
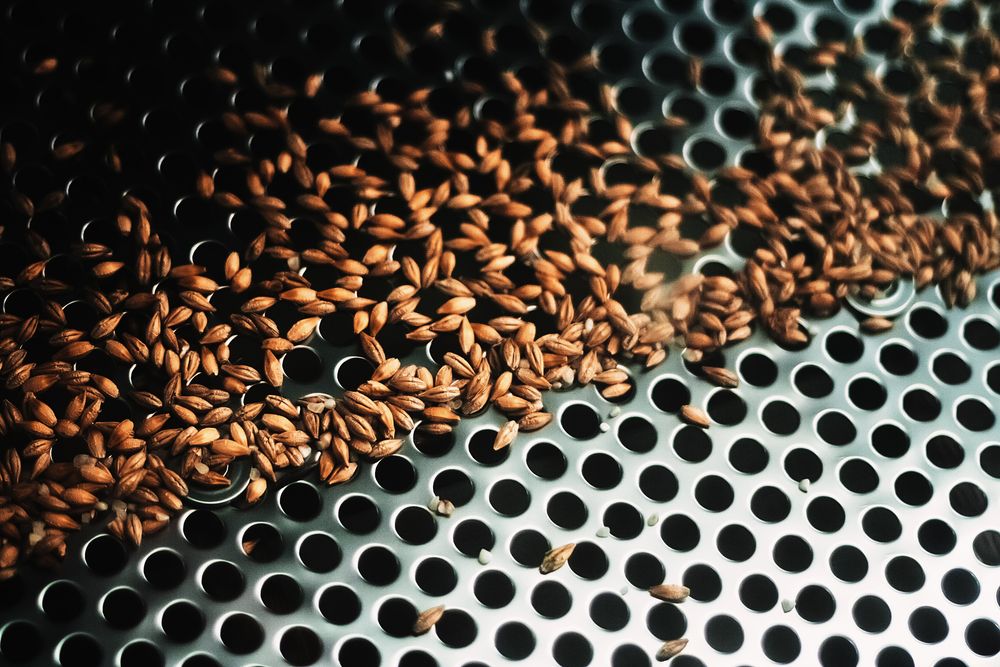
Hendrick Screen produces lauter screens for breweries and distilleries, fulfilling this important component of the lauter tun, where the lautering process occurs. Constructed from industry-standard stainless steel wedge wire — with custom or standard slot opening sizes and screen configurations — our lautering screens provide strength, quality and reliability in this key stage of the brewing or distilling process.
The wedge wire false bottom has been established as the ideal construction to allow the lautering process to occur properly and efficiently. A wedge wire screen is constructed from “V”-shaped stainless steel pieces, set across support beams at regular intervals — typically with openings of .028 inches or .030 inches. Though other slot opening dimensions can be used depending on specific requirements.
The lauter tun wedge wire screen allows the solid grain components of the mash to act as a filter to separate the wort. While the slot openings of the lauter screen false bottom don’t technically act as a filter in the process, they enable the most effective filtration to occur by supporting the grain, which itself becomes the filtering medium — holding back the smallest solids while allowing the wort to pass. A high-quality, tight tolerance construction is necessary to help ensure that the process occurs correctly and uniformly so that the resulting product — whether beer or liquor — is not bittered or otherwise compromised by components that shouldn’t be part of the wort.
Benefits of Wedge Wire
When it comes to brewing or distilling, wedge wire screens are the preferred, state-of-the-art construction for false bottoms. The unique “V” profile of the wire components ensures that solids stay where they belong — out of the wort — while enabling filtration and proper flow of the wort for easy extraction for recirculation, turbidity testing and, eventually, boiling. With wedge wire, clogging is much less likely to occur, meaning that all steps of the lautering process can be carried out efficiently and with minimal need for adjustments or in-process maintenance by staff.
Wedge wire is also the simplest type of lauter screen construction to clean and maintain. Further, it can be easily manufactured in sections to allow for simple addition and removal — whether for maintenance or manway access.
In terms of materials, stainless steel is an ideal choice for lautering screens for several reasons:
- Strength
- Food/beverage grade approval
- Ability to be easily cleaned
- Durability
The temperature fluctuations and durability requirements of lautering (and the brewing or distilling processes overall) mean that the investment in stainless steel is a worthy one, providing a long-lasting, nonreactive surface for the lautering process to occur. At this critical juncture of the process, any small fluctuations in temperature or chemical makeup (such as pH) can compromise the wort. This can create future issues with the boiling process and lead to a beer or liquor that won’t taste as it should, and, in most cases, will be unusable.
With a variety of configurations available for wedge wire lauter screens, they can be effectively used in any scale of brewing or distilling operation — from nano- and microbreweries to much larger commercial endeavors. Moreover, the screens can be produced to have a modular configuration, enabling much easier growth of your brewing or distilling operation as your scale increases. Essentially, the false bottom — from for instance, a 200-gallon lautering tun — can be expanded and added to comprise part of the false bottom for a 500-gallon tun. Thus, your initial investment stays with you and continues to provide a return.
Lautering Screens From Hendrick
At Hendrick, we offer several standard frame options to fix lauter screen sections in place: bottom seal strip, top seal strip or a machine lapped frame. Each is conducive to fast and easy removal for access, cleaning or maintenance. We also feature several perimeter frame options. As mentioned earlier, our standard slot openings are .028 inches and .030 inches, but we are happy to offer our expertise to work with you and determine the right custom configuration for your application, if necessary.
In such a finely tuned process as either brewing or distilling, the importance of high-quality, consistent, reliable components cannot be underestimated. Moreover, production time is critical — both to maintain the integrity of the process and to fulfill commitments to your accounts. Maintenance time and spoiled batches are not only a threat to your bottom line, but also to the quality and reputation of your product.
If you have any further questions about false bottoms for brewing or wedge wire, be sure to contact us today.
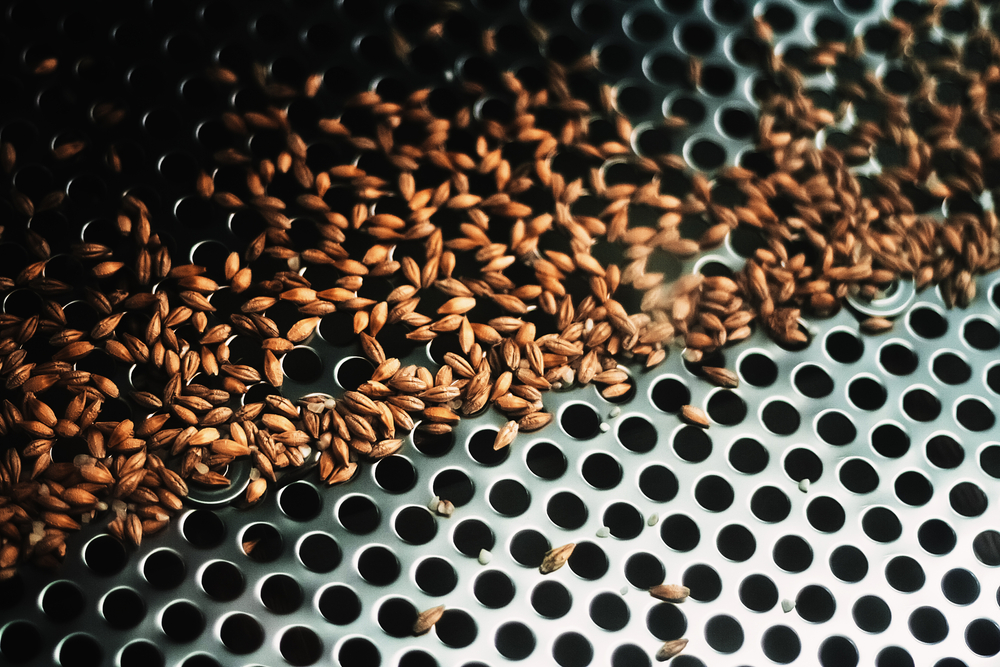